Плазменная наплавка – эффективный способ защиты металлических деталей. Нанесение полимерных покрытий
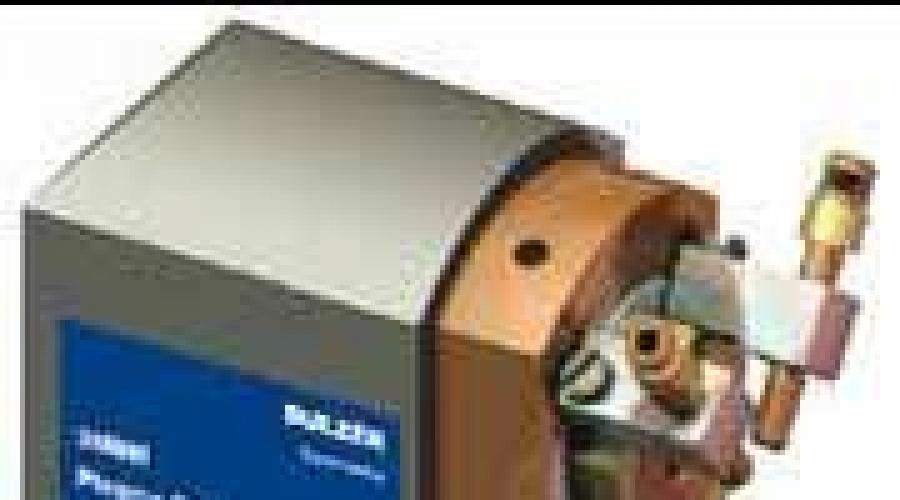
Читайте также
Итак, в чем же состоит принцип плазменного напыления? Во всех устройствах плазменного напыления порошок приобретает температуру и скорость в струе горячего газа, создаваемого плазматроном. В свою очередь, плазматрон или плазменный генератор – это устройство, изобретенное в 1920-х годах, в котором электрическая дуга, горящая между катодом и анодом в ограниченном объеме (сопле), раздувается инертным газом и создает факел высокотемпературного восстановительного пламени.
Чем же так привлекателен этот принцип для решения задач термического напыления? Именно тем, что пламя плазматрона очень горячее и всегда строго восстановительное; присутствие кислорода в плазматроне категорически не допускается из-за быстрого, в противном случае, разрушения материалов электродов (парциальное давление кислорода в плазмообразующих газах определяется их чистотой и должно быть не выше 0,004%). Факел пламени плазматрона, при грамотном его применении, может не только восстановить активную металлическую поверхность из оксидных пленок на напыляемых частицах, но даже и очистить от оксидов саму поверхность субстрата. Подобную возможность предоставляет исключительно метод плазменного напыления.
В отношении плазменного напыления существует, в среде теоретиков и практиков термического напыления, ряд предрассудков, которые, в большинстве случаев, связаны не с процессом как таковым, а с недопониманием сути процесса напыления, недостатками конструкций конкретных устройств и с неправильным их применением. Обсудим эти предрассудки:
1. “Пламя плазмы слишком горячее и пригодно поэтому, только для напыления тугоплавких металлических и оксидных керамических материалов. Слишком высокая температура приводит к испарению части порошка и разрушению карбидов хрома и вольфрама”.
Действительно, температура плазмы может достигать 20.000°C и более, что много выше, чем, например, температура ацетиленокислородного пламени (около 3000°C). Однако, температура пламени имеет очень мало общего с температурой напыляемых частиц. Не углубляясь в физику взаимодействия горячего газа с твердыми частицами, скажем только, что это взаимодействие очень сложное и зависит от большого количества параметров, в числе которых не только температура газа, его скорость, длина факела и размер частиц, но и химические составы газа и частиц. К тому же, решающее значение для передачи тепла от факела к частицам имеет не абсолютная температура пламени, а его светимость. Так, например, более горячее, но почти невидимое водородно-кислородное пламя нагревает частицы гораздо хуже, чем более холодное, но яркое (из-за светящихся нано частиц углерода) ацетилено-кислородное пламя. Светимость факела плазмы зависит от состава плазмообразующего газа, от размера и состава частиц, проходящих сквозь него. Интересно, что во многих случаях эта светимость меньше, чем у ацетиленокислородного пламени и ее приходится увеличивать разными способами, только чтобы придать частицам хотя бы минимальную необходимую температуру. Так как длина пламени газопламенных устройств также часто превышает длину факела плазмы, получается «парадокс»: грубозернистые металлические порошки нагреваются в устройствах порошкового газопламенного напыления сильнее, чем в более мощных и «горячих» устройствах плазменного напыления.
2. “Скорость частиц при плазменном напылении недостаточна для получения плотных покрытий”.
Скорость потока газа и частиц в нем определяется не принципом образования пламени, а исключительно конструкцией устройства. В настоящее время существуют промышленные устройства плазменного напыления с соплом Лаваля, обеспечивающие частицам сверхзвуковую скорость.
3. “Для напыления металлов годятся только дорогостоящие установки вакуумного плазменного напыления, а установки атмосферного плазменного напыления непригодны из-за окисления металлических частиц”.
Подобное утверждение приходится, как ни странно, слышать довольно часто, даже от людей, практически занимающихся плазменным напылением, особенно применительно к покрытиям из MCrAlY для лопаток газовых турбин. На самом же деле, в этом утверждении происходит типичная подмена понятий: чисто металлические покрытия из легкоплавких никелевых сплавов, полученные вакуумным плазменным напылением (VPS), действительно лучше атмосферно напыленных (APS), но не из-за окисления частиц в плазме, а совсем по другой причине, о которой будет рассказано в разделе, посвященном вакуумному плазменному напылению. Окисление же металлических частиц в обоих этих способах происходит одинаково.
Устройства атмосферного плазменного напыления ничем не отличаются от устройств вакуумного плазменного напыления. Разница не в самих устройствах, а в способе организации процесса напыления: атмосферное напыление проводится на воздухе, а при вакуумном напылении и плазматрон, и напыляемая деталь находятся в вакуумной камере под разряжением. Понятно, что атмосферное напыление гораздо доступнее и дешевле вакуумного, к тому же для больших деталей вакуумное напыление становится просто невозможным из-за нереального размера вакуумной камеры. Сами же плазматроны могут использоваться как для атмосферного, так и для вакуумного напыления.
Чтобы понятнее объяснить особенности плазменного напыления, перейдем к рассмотрению разных конструкций, существующих на сегодняшний день.
Установки плазменного напыления
Устройства плазменного напыления отличаются большим разнообразием конструкций. Будем рассматривать их от самых «традиционных» до самых «продвинутых».
Наиболее распространенные устройства, – это устройства с одним катодом и одним анодом, и с вводом порошка снаружи короткого сопла, перпендикулярно к оси пламени.
Принцип действия таких устройств показан на схеме (рисунок 28):
Рис. 28. Принцип плазменного напыления.
Как видно из схемы, короткое сопло плазматрона одновременно является анодом. Порошок вводится снаружи сопла перпендикулярно оси пламени, в непосредственной близости от дуги.
Самое популярное устройство этого типа, – плазматрон 3MB фирмы Sulzer Metco, который, с небольшими модификациями, существует уже больше 40 лет. На рисунке 29 представлены актуальные модели этой серии с максимальной мощностью 40 кВт.
Рис. 29. Плазматрон 3MB.


Несколько более новое и мощное (55 кВт) однокатодное устройство, – плазматрон F4, показанный на рисунке 30.
Рис. 30. Плазматрон F4.
Устройство 9MB, – один из самых мощных однокатодных плазматронов традиционного типа (80 кВт при токе 1000 А и напряжении 80 В) производится также фирмой Sulzer Metco (рисунок 31):
Рис. 31. Плазматрон 9MB
Традиционные однокатодные плазматроны других фирм мало отличаются от плазматронов Sulzer Metco: все они работают при относительно малом расходе газов, низком (< 100 В) напряжении и большом (до 1000 А) токе дуги. Ни один из традиционных плазматронов не позволяет достичь частицам скорости звука.
Достоинством плазматронов с небольшим расходом газов является возможность придания частицам очень высокой температуры (> 4000°C) из-за относительно долгого времени их пребывания в горячей зоне пламени рядом с дугой. Столь высокие температуры частиц позволяют расплавить практически любые керамические и металлические материалы.
Развитие техники плазменного напыления в последние двадцать лет идет по пути увеличения скорости частиц. Для придания частицам большей скорости необходимо увеличить давление плазмообразующих газов перед соплом, что автоматически приводит к повышению расхода газов и росту напряжения дуги.
Современное, мощное (до 85 кВт, ток до 379 А, напряжение до 223 В) устройство с одним катодом и анодом – это плазматрон 100HE американской фирмы Progressive Technologies Inc., который, благодаря большому давлению и расходу плазмообразующих газов, позволяет достичь скоростей частиц – близких к скорости звука (рисунок 32):
Рис. 32. Плазматрон 100HE.
Из-за высокой скорости плазмообразующего газа уменьшается время пребывания частиц в горячей зоне пламени и, соответственно, их температура. Для противодействия этому необходимо увеличивать мощность дуги и использовать в плазмообразующем газе большое количество водорода, который, благодаря процессу диссоциации-ассоциации молекул, удлиняет горячую зону пламени. Таким образом, плазматрон 100HE реализует температуру частиц, с размером 20-30 мкм, выше 2300°C при скорости около 250 м/сек, что делает возможным напылять покрытия из Cr 3 C 2 – NiCr, Cr 2 O 3 и Al 2 O 3 с малой пористостью.
Вторым направлением развития, в комбинации с увеличением расхода газов, является деление одной дуги на три части, которое позволяет улучшить стабильность и равномерность факела пламени, уменьшить износ электродов и увеличить суммарную мощность пламени. Типичным примером такого устройства является новейший плазматрон TriplexPro TM -210 фирмы Sulzer Metco с одним анодом и тремя катодами, максимальной мощностью 100 кВт (рисунок 33):
Рис. 33. Плазматрон TriplexPro TM .
1 – задняя часть корпуса; 2 – анодный стек; 3 – передняя часть корпуса; 4 – изолятор; 5 – накидная гайка; 6 – три катода в керамическом блоке; 7 – элемент анодного стека; 8 – канал плазмы; 9 – насадка с тремя порошковыми дюзами.
Технология Triplex от Sulzer Metco вошла в практику термического напыления в 90-х годах. Эти устройство обладают, по сравнению с плазматронами с одной дугой, существенно большим ресурсом и стабильностью результатов напыления. Для многих коммерческих порошков плазматроны Triplex позволяют также улучшить производительность и КПД напыления при сохранении качества покрытия.
Фирмой GTV GmbH выпущено, в обход патента Sulzer Metco на трехкатодные плазматроны, устройство GTV Delta с одним катодом и тремя анодами, которое, в принципе, является ухудшенной компиляцией TriplexPro (рисунок 34):
Рис. 34. Плазматрон GTV Delta.
Последнее, третье направление развития – это отказ от радиального ввода порошка в пользу гораздо более рационального – осевого. Ключевой элемент конструкции плазматрона с осевым вводом порошка – Convergens был изобретен в 1994 году американцем Люсьеном Богданом Дэльча (Delcea, Lucian Bogdan).
В настоящее время существует только одно подобное устройство, – плазматрон Axial III, максимальной мощностью 150 кВт, производства канадской фирмы Mettech, которое объединяет собой все три направления развития (большой расход газов, три дуги и осевой ввод порошка). Установки плазменного напыления с плазматроном Axial III производятся и распространяются также немецкой фирмой Thermico GmbH.
На рисунках 35, 36 и 37 изображено само устройство Axial III и его конструктивная схема:
Рис. 35. Плазматрон Axial III.
Рис. 36. Вид на устройство Axial III со стороны сопла.
Рис. 37. Принципиальная схема Axial III.
Все современные установки плазменного напыления являются автоматическими, то есть, управление источниками тока, системой водяного охлаждения и расходом газов регулируется системой ЧПУ с визуализацией и сохранением рецептов на компьютере. Так, например, плазматрон Axial III поставляется фирмой Thermico GmbH в комплекте с компьютеризированной системой управления, самостоятельно проводящей зажигание дуг и выход на рабочий режим, выбор рецептов напыления, и осуществляющей контроль всех основных параметров: расхода трех плазмообразующих газов (аргона, азота и водорода), токов дуг, параметров системы водяного охлаждения. Эта же автоматическая система управляет и порошковым питателем.
О порошковом питателе Thermico нужно сказать особо. Это, наиболее «продвинутое» на сегодняшний день в мире устройство позволяет не только постоянно регулировать массовый расход порошка и расход несущего газа (азота или аргона), но и допускает использование тонкозернистых порошков с плохой сыпучестью, непригодных, например, для питателей фирмы Sulzer Metco.
Автор лично, в течение долгого времени работал с плазматроном Axial III и может из своего опыта сказать, что несмотря на некоторые конструктивные недоработки, этот плазматрон представляет собой самое прогрессивное устройство термического напыления, объединяющее достоинства высокоскоростного напыления с высокой температурой строго восстановительного пламени. Главное же достоинство Axial III состоит в осевом вводе порошка.
Достоинства осевого ввода порошка
Осевой ввод порошка – это качественный скачок в технике плазменного напыления. Дело тут не только в том, что при осевом вводе значительно уменьшаются потери порошка, но и в том, что открываются возможности напыления совсем других порошковых материалов, непригодных для радиального ввода. Так как этот аспект является принципиально важным для понимания следующих разделов, остановимся на нем подробнее.
Итак, что же происходит при радиальном вводе порошка в струю пламени на выходе из сопла? Перечислим недостатки такого ввода:
- Для радиального ввода пригодны только очень узкофракционные порошки, для которых необходимо точно подбирать давление несущего газа. Что это значит?: При недостаточном давлении несущего газа частицы порошка будут «отскакивать» от струи пламени, при слишком высоком давлении несущего газа они будут «простреливать» это пламя насквозь; если же порошок состоит из частиц разного размера, то подобрать «правильное» давление несущего газа в принципе невозможно: самые мелкие частицы будут всегда «отскакивать», а самые крупные – всегда «простреливать», то есть, ни тех ни других частиц в напыляемом покрытии не будет, а будут только какие-то «средние» частицы. Особенно трудно вводятся мелкозернистые порошки из-за их повышенного рассеяния несущим газом (типичное облако пыли вокруг факела).
- При радиальном вводе порошка нельзя использовать в порошковой смеси не только частицы разных размеров, но и разных плотностей (разных масс) по той же причине: более тяжелые частицы пролетают сквозь пламя легче более легких. Таким образом, попытка использования сложных порошковых смесей приведет к искажению состава покрытия по сравнению с составом порошковой смеси.
- Увеличение скорости плазмообразующих газов усложняет радиальный ввод порошка, так как дополнительно сужаются интервалы необходимых давлений несущего газа и распределения частиц по размерам. На практике это означает следующее: чем выше скорость пламени, тем меньше КПД напыления при радиальном вводе порошка. Ввести же весь порошок в пламя без потерь невозможно ни при каких обстоятельствах.
- Расположение порошковых дюз рядом с горячей зоной пламени вызывает их разогрев, компенсирующийся только охлаждением газом, несущим порошок. Если же скорости охлаждающего газа недостаточно для охлаждения, то частицы порошка могут налипать на края отверстия дюз, образуя натеки. Налипшие куски периодически отрываются от дюзы, попадают в пламя и вызывают характерный дефект – «плевание», приводящий к образованию грубых пористых включений в покрытии. Так как скорость истечения несущего газа строго связана с параметрами пламени (см. пункт 1), то возникает проблема: для некоторых порошков просто не существует параметров, убирающих эффект «плевания», особенно если эти порошки легкоплавкие и/или мелкозернистые.
Переход на осевое введение порошка позволяет полностью избавиться от вышеперечисленных проблем:
- Давление и скорость несущего газа больше не привязаны к параметрам пламени и порошка. Единственное условие, – давление несущего газа должно быть несколько выше давления плазмообразующего газа в сопле в месте ввода порошка. За счет осевого ввода, любой порошок полностью захватывается пламенем.
- Всегда можно подобрать такое давление несущего газа, при котором «плевания», связанного с налипанием порошка на край отверстия порошковой дюзы происходить не будет.
- Возможно использование порошковых смесей любой сложности и фракционного состава. Частицы разных размеров будут приобретать различные скорости и температуры, но все, в итоге, примут участие в образовании покрытия. То, что мелкие частицы при осевом вводе в пламя плазмы становятся значительно горячее крупных, открывает новые возможности для дизайна порошковых смесей. Созданию таких полифракционных композиций посвящена основная часть этой книги.
Автору очень повезло, что в его распоряжении в течение многих лет находился плазматрон Axial III с осевым вводом порошка. Если бы не это, то создание новых многокомпонентных покрытий было бы просто невозможно.
Сводная таблица устройств термического напыления
Для обобщения, прямого сравнения и систематизации всех способов термического напыления сопоставим свойства типичных устройств, а также их примерные цены в одной таблице (таблица 2):
Таблица 2. Сравнение устройств термического напыления .
Свойства и характеристики | * Способы термического напыления | |||||||
1 | 2 | 3 | 4 | 5 | 6 | 7 | 8 | |
Использование порошка или проволоки | проволока | порошок | проволока | порошок | порошок | порошок | проволока | порошок |
Максимальная скорость напыляемых частиц, м/сек | 100 | 50 | 200 | 800 | 1200 | 1000 | 100 | 400 |
Максимальная температура напыляемых частиц, °C | 2800 | 2500 | 1700 | 1500 | 600 | 1200 | > 4000 | > 4000 |
Размер частиц, образующих покрытие, мкм | 0,1 – 1000 | 10 – 150 | 0,1 – 1000 | 10 – 100 | 10 – 100 | 10 – 100 | 0,1 – 1000 | 1 – 50 |
КПД напыления по напыляемому материалу | — | + | — | +++ | +++ | +++ | — | ++ |
КПД напыления по расходу | – | +++ | — | — | — | — | ++ | – |
Минимальная пористость покрытия, об.% | 10-15 | 10-25 | 5-10 | 2-3 | < 1 | < 1 | 5-10 | 0,5-3 |
Термическая мощность устройств, кВт | 10-30 | 10-50 | 30-100 | 50-250 | 30-85 | < 20 | 20-150 | 25-150 |
Производительность напыления, кг/час | 2-5 | 5-10 | 2-5 | 5-10 | 10-20 | < 1 | 10-30 | 2-5 |
Распространенность коммерческих устройств и запчастей на мировом рынке | Много устройств | Много устройств | Мало устройств | Много устройств | Мало устройств | Нет устройств | Много устройств | Много устройств |
Мобильность устройств | +++ | +++ | – | – | +++ для – для остальных | — | +++ | – для APS |
Шумность устройств | — | +++ | — | — | — | — | — | — |
Эмиссия паров и тонкой пыли | — | ++ | — | ++ | +++ | ++ | — | – |
Цена отдельных устройств, € | 2.000- | 2.000- | 10.000- | 10.000- | 10.000- | нет | 10.000- | 5.000- |
Цена автоматизированных установок без периферии, € | нет | 30.000- | нет | 100.000- | 100.000- | нет | нет | 100.000- |
Цена автоматизированных установок с периферией «под ключ»: звукозащитной кабиной, фильтровентиляционной установкой, роботом и т.д., € | нет | 100.000- | нет | 200.000- | 200.000- | нет | нет | 200.000- |
Сравнительная стоимость эксплуатации с учетом расходных материалов (кроме порошков и проволок), ресурса устройств и запасных частей, | 10-15 | 5-15 | 30-60 | 40-100 | 40-100 | > 100 | 5-30 | 30-150 |
* Нумерация способов:
- Газопламенное напыление проволокой
- Газопламенное напыление порошком
- Сверхзвуковое газопламенное напыление проволокой
- Сверхзвуковое газопламенное напыление порошком (HVOF и HVAF)
- Холодное напыление порошком
- Детонационное напыление порошком
- Электродуговое напыление проволокой
- Плазменное напыление порошком (APS и VPS)
Важно отметить, что резервы свойств исходных материалов и общеизвестных технологий, используемых при изготовлении изнашиваемых деталей, с точки зрения повышения износостойкости, практически полностью израсходованы.
Одним из перспективных направлений на пути создания высоконадежных, долговечных и конкурентоспособных изнашиваемых деталей является применение современных технологий нанесения функциональных покрытий. В мировой практике известны три основных наиболее часто применяемых метода нанесения покрытий – это технологии наплавки, напыления и осаждения. Трудности выбора оптимального метода, стоящие перед технологами машиностроительных производств, осложняются большим количеством подвидов вышеназванных технологий, многовариантностью режимов, а также многообразием применяемых присадочных и других вспомогательных материалов. Поэтому знание основных характеристик, достоинств и недостатков данных процессов позволит ориентироваться в выборе технологий для решения конкретных производственных задач.
Рис. 1 Напыление вала
Основным отличительным признаком метода нанесения является толщина покрытия: для процессов наплавки – это более 1 мм, для напыления – менее 1 мм, для осаждения – менее 10 мкм. В данной статье приведены сравнительные характеристики наиболее часто используемых газотермических методов, проводимых при атмосферном давлении, дано определение этих методов, рассмотрена их классификация, преимущества и недостатки.
Технологии наплавки
Наплавка – нанесение покрытий слоями толщиной в несколько миллиметров из расплавленного присадочного материала на оплавленную металлическую поверхность изделия. В зависимости от вида источника нагрева рассматриваемых газотермических процессов наплавка может производиться при помощи теплоты газового пламени (газопламенная наплавка), электрической дуги (электродуговая наплавка в среде защитного газа) или сжатой дуги (плазменная наплавка).
Рис. 2 ПНН клапана
Назначение наплавки – изготовление деталей с износо и коррозионностойкими свойствами поверхности, а также восстановление размеров изношенных и бракованных деталей за счет нанесения покрытий, обладающих высокой плотностью и прочностью сцепления с изделием, работающих в условиях высоких динамических, знакопеременных нагрузок или подверженных интенсивному абразивному изнашиванию.
Преимущества процессов наплавки:
- отсутствие ограничений по размерам наплавляемых зон;
- возможность нанесения покрытий различных толщин;
- возможность получения требуемых размеров восстанавливаемых деталей путем нанесения материала того же состава, что и основной металл;
- использование не только для восстановления размеров изношенных деталей, но и для ремонта изделий за счет ликвидации локальных трещин, пор и других дефектов;
- возможность (применительно к плазменной наплавке) ведения процесса на постоянном токе обратной полярности, повышающим качество и стабильность свойств биметаллических соединений за счет эффекта катодной очистки, проявляющемся в удалении окисных и адсорбированных пленок и улучшении смачивания жидким металлом обрабатываемой поверхности; более низкого тепловложения по сравнению с наплавкой на токе прямой полярности и, как следствие, отсутствие или минимальное расплавление подложки;
- возможность многократного проведения процесса и, следовательно, высокая ремонтоспособность наплавляемых деталей;
- высокая производительность и легкость автоматизации процесса;
- относительная простота и мобильность оборудования.
Недостатки технологий наплавки:
- возможность изменения свойств наплавленного покрытия изза перехода в него элементов основного металла;
- изменение химического состава основного и наплавленного металла вследствие окисления легирующих элементов и основы металла;
- возможность структурных превращений в основном металле, в частности, образование крупнозернистой структуры, новых хрупких фаз;
- возникновение деформаций в наплавленных изделиях за счет значительного термического воздействия;
- образование больших растягивающих напряжений в поверхностном слое детали, достигающих 500 МПа;
- снижение характеристик сопротивления усталости наплавленных изделий;
- возможность возникновения трещин в наплавленном металле и зоне термического влияния, и, как следствие, более ограниченный, чем, например, при напылении, выбор сочетаний основного и наплавленного металлов;
- обязательное использование в отдельных случаях предварительного нагрева и медленного остывания наплавляемого изделия, что увеличивает длительность процесса;
- наличие больших припусков на механическую обработку и, как следствие, существенные потери металла наплавки;
- трудоемкость механической обработки наплавленного слоя большой толщины;
- требования преимущественного расположения наплавляемой поверхности в горизонтальном положении (необходимость применения наплавки в нижнем положении при использовании порошковых металлов);
- трудность наплавки мелких изделий сложной формы.
Таблица 1. Технико-экономические показатели методов наплавки
Метод
наплавки |
Производительность
метода |
Толщина покрытия | Припуск на обработку | Доля основного металла в наплавленном | Прочность сцепления | Деформация детали после наплавки |
Снижение сопротивления усталости | Коэффициент производительности,
К п |
Коэффициент техникоэкономической эффективности,
К э |
|
кг/ч | см 2 /мин | мм | мм | % | МПа | % | ||||
Газопламенный | 0,15 2,0 | 1 3 | 0,53,5 | 0,40,8 | 530 | 480 | Значительная | 25 | 0,70,6 | 0,14 |
В среде CO 2 | 1,5 4,5 | 18 36 | 0,53,5 | 0,71,3 | 1245 | 550 | Значительная | 15 | 1,81,7 | 0,40 |
В среде Ar | 0,3 3,6 | 12 26 | 0,52,5 | 0,40,9 | 625 | 450 | Пониженная | 25 | 2,11,7 | 0,17 |
Плазменный | 1 12 | 45 72 | 0,55,0 | 0,40,9 | 030 | 490 | Пониженная | 12 | 2,21,9 | 0,56 |
Техникоэкономические показатели рассматриваемых способов наплавки представлены в табл. 1 , где даны показатели для покрытий толщиной 1 мм. Коэффициент производительности – К п рассчитан как отношение основного времени, затраченного на восстановление условной детали ручным дуговым способом t р.н., к основному времени восстановления условной детали сравниваемым способом t i: К п =t р.н. /t i . За основное время восстановления условной детали приняты затраты времени, включающие предварительную и последующую механические обработки и нанесение покрытия. Коэффициент техникоэкономической эффективности – К э определялся с учетом производительности и экономичности способа восстановления условной детали: К э =К п ·Э а /100, где Э а – экономия при восстановлении условной детали, %.
Использование конкретного способа наплавки из рассмотренных обусловлено условиями производства, количеством, формой и размерами наплавляемых деталей, допустимой долей участия основного металла в наплавленном, техникоэкономическими показателями, а для восстановительной наплавки – величиной износа.
Выбор типа наплавленного металла и, следовательно, марки присадочного материала производится в соответствии с видом рабочего нагружения наплавляемой детали. Основными видами нагружения деталей машин и инструмента являются: абразивное, ударноабразивное, гидроабразивное, контактноударное, термомеханическое, трение металла о металл, кавитационное, коррозионное. Детали машин чаще всего испытывают одновременно несколько видов нагружения. Поэтому при выборе типа наплавленного металла ориентируются на преобладающий вид износа.
Рис. 3 Осаждение покрытия на фрезу
Из сравнительного анализа рассмотренных методов очевидно преимущество процесса плазменной наплавки, вследствие его высокой производительности, незначительного припуска на механическую обработку, минимальной доли основного металла в наплавленном, наименьшему снижению сопротивления усталости. Особенно эффективен процесс плазменнопорошковой наплавки, позволяющий обеспечить точно заданную глубину проплавления и толщину покрытия, высокую равномерность по толщине слоя, возможность обеспечения необходимых состава, структуры и свойств уже в первом слое металла наплавки, высокую степень автоматизации, малые остаточные напряжения и деформации, отсутствие разбавления наплавляемого покрытия основным металлом.
Технологии напыления
Напыление – процесс, заключающийся в нагреве распыляемого материала высокотемпературным источником, образовании двухфазного газопорошкового потока и формировании покрытия на поверхности изделия толщиной менее 1 мм.
В зависимости от вида используемого источника энергии процессы напыления подразделяются на:
- газопламенные, в которых используется тепло при сгорании горючих газов (ацетилена, пропанбутана, водорода, метана, природного газа и др.) в смеси с кислородом или сжатым воздухом;
- электродуговые, где осуществляется плавление проволоки электрической дугой и распыление расплавленного металла сжатым воздухом;
- детонационные, использующие энергию детонации газовых смесей (кислород + горючий газ), в которых перенос и нагрев частиц осуществляется ударной волной, образующейся в результате взрыва горючей смеси и выделении при этом теплоты;
- плазменные, где плавление наносимого порошкового материала осуществляется в плазменной струе;
- высокоскоростные, где порошок подается в камеру сгорания, в которой обеспечивается горение топлива содержащего кислород и горючие газы (керосин, водород, пропан, метан) с последующим прохождением порошка и газов через расширяющееся сопло.
Метод напыления |
Вид напыляемого материала |
Оптимальная толщина покрытия |
Температура пламени, дуги, детонации, струи |
Скорость истечения пламени, дуги, детонации, струи |
Скорость частиц |
Прочность сцепления покрытия с основой |
Пористость покрытия |
Производительность процесса |
Коэффициент использования материала |
Уровень шума |
||
металл |
керамика |
|||||||||||
кг / ч |
||||||||||||
Газопламенный |
порошок, проволока |
3463 (С 2 Н 2 +О 2) |
||||||||||
Электродуговой |
проволока |
|||||||||||
Детонационный |
||||||||||||
Плазменный |
в инертных средах |
порошок, проволока |
0,58 (2060 кВт) |
|||||||||
в активных средах |
||||||||||||
в разряженных средах |
||||||||||||
Высокоcкоростной |
Назначение процессов напыления – нанесение защитных покрытий заданных свойств минимальной толщиной от 0,05 мм и восстановление размеров изношенных и бракованных поверхностей. Техникоэкономические показатели процессов напыления представлены в табл. 2 .
Преимущества технологий напыления:
- универсальность процессов, позволяющая наносить покрытия разного функционального назначения, а также для восстановления размеров изношенных деталей;
- малое термическое воздействие на напыляемую основу (температура ее нагрева не превышает 100150 °С), позволяющее исключить нежелательные для нее структурные превращения, избежать деформаций и изменения размеров изделий;
- возможность нанесения покрытий на изделия, изготовленные практически из любого материала;
- отсутствие ограничений по размерам напыляемых изделий;
- возможность нанесения покрытий на локальные поверхности;
- возможность нанесения многослойных покрытий разнородными материалами;
- высокая технологичность процесса, в связи с гибкостью регулирования параметров режима;
- возможность получения регламентируемой однородной пористости покрытия для использования в условиях работы со смазкой поверхностей скольжения;
- положительное влияние на усталостную прочность основы, за счет получения при напылении слоистой структуры покрытия, в отличие от столбчатой, образующейся при осаждении из газовой или паровой фазы, диффузионном насыщении;
- нанесение равномерного покрытия с минимальными припусками для последующей механической обработки;
- возможность эксплуатации в отдельных случаях напыленных деталей без последующей механической обработки;
- возможность использования напыления для формообразования деталей (напыление производят на поверхности формыоправки, которую после окончания процесса удаляют; остается оболочка из напыленного материала);
- высокая производительность процесса напыления;
- возможность автоматизации процесса.
Недостатки процессов напыления:
- нестойкость напыленных покрытий к ударным механическим нагрузкам;
- анизотропия свойств напыленных покрытий;
- низкий коэффициент использования напыленного материала при нанесении покрытий на мелкие детали;
- обязательное использование перед процессом напыления активационной обработки (например, абразивноструйной), что увеличивает длительность и трудоемкость процесса;
- выделение аэрозолей напыляемого материала и побочных газов, требует использования мощной вытяжной вентиляции;
- повышенный уровень шума, а в случаях, связанных с электрической дугой – ультрафиолетового излучения.
Технологии осаждения
Осаждение – это методы нанесения защитных покрытий микронной толщины (менее 10 мкм), характеризующиеся конденсацией на поверхности изделий компонентов паровой или газовой фазы в условиях обработки частицами высоких энергий в вакууме или плазменными струями при атмосферном давлении.
Отличительными свойствами методов является обеспечение высокой адгезионной прочности покрытия к основе за счет применения физических процессов подготовки и активации поверхности (нагрева и предварительной очистки поверхностей тлеющим разрядом, бомбардировкой ионами инертных газов).
Процесс формирования покрытий осуществляется за счет обработки ионами в процессе конденсации, осаждения высокоэнергетических ионов, а также атомов и молекул с участием плазмохимических процессов.
Процессы осаждения подразделяются на:
- плазменные, заключающиеся в нанесении покрытий при атмосферном давлении и являющиеся продуктами плазмохимических реакций реагентов, прошедших через дуговой или высокочастотный плазмотрон;
- ионноплазменные, происходящие в вакууме: необходимый для получения покрытий материал переводится из твердой в газовую фазу распылением мишени энергетическими ионами или испарением катода, добавкой реакционных газов;
- ионнолучевые, аналогичные ионноплазменным, в которых дополнительно используются электроннолучевые пушки.
Назначение процессов осаждения – изготовление деталей машин и механизмов, технологической оснастки и инструмента, предусматривающее финишный способ нанесения тонкопленочных покрытий различного применения.
Рассмотрим сравнительные характеристики двух основных процессов осаждения покрытий микронной толщины при помощи использования плазменных струй, истекающих при атмосферном давлении – высокочастотного плазменного нанесения износостойких покрытий и электродугового плазменного нанесения тонкопленочных покрытий (технология финишного плазменного упрочнения – ФПУ).
Процесс высокочастотного плазменного нанесения тонкопленочных покрытий осуществляется на установке «Плазма401», предназначенной для упрочнения элементов штампов холодного деформирования из инструментальных сталей типа Х12М и У10 и различного режущего инструмента. Нанесение износостойких покрытий осуществляется при атмосферном давлении при помощи высокочастотного индукционного (ВЧИ) плазмотрона, позволяющего получать объемные потоки спектрально чистой плазмы благодаря отсутствию эрозирующих электродов. Элементы покрытия образуются за счет разогрева газоразрядной плазмой пучка кварцевых стержней. Одновременно в камеру ВЧИплазмотрона подается реакционный газ – аргон, барботируемый через этиловый спирт. В зоне высоких температур пары реакционных веществ разлагаются на исходные компоненты, а при снижении температуры происходит восстановление элементов с плазмохимическим синтезом кремнийуглеродистых соединений, которые уносятся плазмообразующим газом и осаждаются на напыляемой детали.
Сущность технологии электродугового плазменного нанесения тонкопленочных покрытий (процесс финишного плазменного упрочнения – ФПУ) состоит в нанесении износостойкого покрытия с возможностью или отсутствием одновременного осуществления процесса повторной плазменной закалки приповерхностного слоя (на глубину нескольких микрометров). Покрытие является продуктом плазмохимических реакций реагентов, прошедших через дуговой плазмотрон. Закалка происходит за счет локального воздействия высококонцентрированной плазменной струи.
Цель ФПУ– изготовление инструмента, штампов, прессформ, ножей, фильер, подшипников и др. деталей машин со специальными свойствами поверхности: износостойкостью, антифрикционностью, коррозионностойкостью, жаростойкостью, разгаростойкостью, антисхватыванием, стойкостью против фреттингкоррозии.
Эффект от ФПУ достигается за счет изменения физикомеханических свойств поверхностного слоя: увеличения микротвердости, уменьшения коэффициента трения, создания сжимающих напряжений, залечивания микродефектов, образования на поверхности диэлектрического и жаростойкого пленочного покрытия с низким коэффициентом теплопроводности, химической инертностью и специфической топографией поверхности.
Оборудование для ФПУ включает в себя источник тока, блок аппаратуры с жидкостным дозатором, плазмотроном и плазмохимическим генератором.
Технологический процесс ФПУ проводится при атмосферном давлении и состоит из операций предварительной очистки (любым известным методом) и непосредственно упрочнения обрабатываемой поверхности путем взаимного перемещения изделия и плазмотрона. Температура нагрева деталей при ФПУ не превышает 100120 0 С. Параметры шероховатости поверхности после ФПУ не изменяются. В качестве плазмообразующего газа используется аргон, исходным материалом для прохождения плазмохимических реакций и образования покрытия является жидкий препарат СЕТОЛ. Его расход не превышает 0,5 г/ч (не более 0,5 литра в год).
По сравнению с аналогами – ионноплазменным напылением, лазерным и электроискровым упрочнением, эпиламированием, нанесением кластерных покрытий процесс ФПУ имеет следующие преимущества:
- высокая воспроизводимость и стабильность упрочнения за счет двойного эффекта – от износостойкого покрытия и структурных изменений в тонком приповерхностном слое;
- проведение процесса упрочнения на воздухе при температуре окружающей среды не требует применения вакуумных или других камер и ванн;
- вследствие нанесения тонкопленочного покрытия (толщиной не более 3 микрометров), укладывающегося в допуски на размеры деталей, процесс упрочнения используется в качестве окончательной финишной операции;
- отсутствие изменений параметров шероховатости поверхности после процесса упрочнения;
- минимальный нагрев в процессе обработки (не более 100120 о С) не вызывает деформаций деталей, а также позволяет упрочнять инструментальные стали с низкой температурой отпуска;
- возможность упрочнения локальных (по глубине и площади) объемов деталей в местах износа с сохранением исходных свойств материала в остальном объеме;
- тонкопленочное покрытие по микротвердости наиболее близко к алмазоподобным покрытиям;
- образующиеся на поверхности после ФПУ сжимающие остаточные напряжения при циклической нагрузке повышают усталостную прочность изделия (для сравнения: после операции шлифования возникают растягивающие напряжения, ведущие к снижению усталостной прочности);
- высокая адгезионная прочность сцепления покрытия с основой обеспечивает максимальную сопротивляемость истиранию (в том числе – при взаимодействии инструмента с обрабатываемым материалом);
- низкий коэффициент трения способствует подавлению процессов наростообразования при резании или налипания при штамповке и прессовании;
- формирование специфического микрорельефа поверхности способствует эффективному его заполнению смазочноохлаждающей жидкостью при эксплуатации инструмента и деталей машин;
- образующееся на поверхности тонкопленочное аморфное (стеклообразное) покрытие защищает изделие от воздействия высокой температуры (испытания на высокотемпературную воздушную коррозию в течение 100 часов при температуре 800 о С);
- высокая производительность упрочнения (время обработки, например, кромок вырубного штампа средних размеров может составлять несколько минут);
- простота операций по очистке и обезжириванию перед упрочнением (отсутствие специальной предварительной подготовки);
- возможность упрочнения поверхностей деталей любых габаритов в ручном или автоматическом режимах;
- минимальное потребление и низкая стоимость расходных материалов;
- низкая потребляемая мощность установки для упрочнения – менее 6 кВт;
- незначительная площадь, занимаемая оборудованием – 13 м 2 ;
- малогабаритный плазмотрон для упрочнения (массой около 1 кг) может быть легко закреплен на манипуляторе, в руке робота, а также позволяет вести обработку вручную;
- транспортабельность и маневренность оборудования (масса порядка 100 кг);
- экологическая чистота процесса в связи с отсутствием отходов при упрочнении;
- минимальный уровень шума, не требующий специальных мер защиты;
- в отличие от методов упрочнения с использованием поверхностноактивных веществ в данной технологии отсутствуют особые требования к помещению, нет контактирования с токсичными материалами, не требуется затрат времени на выдержку в растворах и сушку обработанных деталей;
- возможность образования профилированных углублений путем обработки поверхности методом ФПУ и образования рабочих зазоров 23 мкм (например, для газодинамических подшипников);
- в отличие от избирательного переноса в процессе трения при ФПУ происходит принудительное образование в зоне фрикционного контакта тонкой неокисляющейся аморфной пленки с низким сопротивлением сдвигу, неспособной накапливать дислокации (дефекты) при деформации.
Тополянский П.А.,
Тополянский А.П.
НПФ «Плазмацентр»
(СанктПетербург)
Установка для создания плазменного покрытия используется в энергетическом и авиационном машиностроении для создания керамических функциональных покрытий.
Назначение комплекса:
Нанесение коррозионностойких, износостойких, уплотнительных, теплозащитных покрытий.
Характеристики установки:
ТСЗП MF-P-1000 работает на смеси газов: основной - аргон, дополнительный - азот, водород или гелий.
Состав оборудования
Система управления смонтирована в пылезащищенном шкафу
Модульная система контроллера позволяет использовать огромный спектр дополнительных коммуникационных и функциональных модулей, которые расширяют возможности ЦПУ.
Установка управляется с панели оператора. На ней отображаются параметры протекающих процессов, и осуществляется их контроль. Машинные данные преобразуются в кривые, гистограммы и графические объекты, которые меняют свой вид в зависимости от выбранной программы и от состояния процесса. Кроме того, выводимые на панель сообщения о неисправностях, обеспечивают оператора важной информацией о состоянии управляемой установки. С нее могут контролироваться все технологические параметры процесса, и в памяти могут оставаться до ста технологических программ.
Пульт управления установкой плазменного напыления
Блок газоподготовки для подачи газа в плазмотрон
![]() ![]() |
Блок газоподготовки включает:
Все данные с блока газоподготовки выводятся на панель оператора. Плазмообразующие газы: аргон, водород, азот, гелий. Система позволяет работать с одним или двумя плазмообразующими газами.Транспортирующий газ: аргон |
Источник питания плазмотрона PPC 2002
![]() |
Источник постоянного тока PPC 2002 выполнен по принципу высококачественного инвертирования постоянного тока, что обеспечивает плавное нарастание тока дуги. Техническая характеристика Габаритные размеры |
![]() |
Порошковый дозатор состоит из двух миксеров, двух бункеров, двух дисковых приводов регулирования подачи порошка. Газовая система питателя составлена из предохранительных клапанов, двух ротаметров, электромагнитных вентилей, шлангов и дросселей. Управление работой осуществляется на базе контроллера Simatic S7-300. Питатель порошка может работать в автономном режиме или управляться с центральной панели оператора. Емкость бункеров (колб) может быть 1,5 или 5 литров — их количество и объем оговаривается при подписании договора. Техническая характеристикаПроизводительность одной колбы до 6 кг/час в зависимости от типа порошка. Габаритные размеры |
Габаритные размеры
Технические характеристики плазмотронов
Модель F4 – одна из самых распространенных. Доступны различные разъемы для подключения водяного охлаждения. Установка может поставляться с ручкой для ручного напыления. Устройство универсально с точки зрения широты задаваемых параметров — материала, твердости, пористости и шероховатости.
Для повышения качества напыления могут применяться различные сопла.
- Обычно эксплуатируются с плазменными установками мощностью до 55 Квт
- Обычно эксплуатируются с плазмообразующими газами Ar/H 2 , для некторых материалов могут применяться смеси Ar/He, Ar/N 2 или N 2 /H 2 ;
Плазмотрон F6
Аттестован авиацией, основан на классической модели F4. При сохранении базовой геометрии и основных параметров напыления, улучшенная система охлаждения позволяет существенно повысить производительность и продлить ресурс анода/катода. Кроме того, все части выполнены из бронзы, без применения пайки. Быстросъемные соединения позволяют осуществлять замену электродов за секунды. Фитинги шлангов водяного охлаждения соединены с базовой пластиной и не повреждаются в процессе замены электродов.
Для повышения качества напыления используются различные сопла.
- Обычно эксплуатируются с плазменными установками мощностью до 55 Квт
- с плазмообразующими газами Ar/H2, для некоторых материалов могут применяться смеси Ar/He, Ar/N2 или N2/H2;
- Для увеличения качества напыления используются различные сопла: сопла Лаваля позволяют напыление с более высокими эффективностью и коeффициентом использования материала при пониженном уровне шума.
Плазмотрон Delta
Использование трех анодов и одного катода позволяет объединить преимущества всех известных технологий. Стабильная дуга обеспечивает производительность до 300 грамм порошка в минуту.
Модель дельта состоит из сопла, каскада, малоизнашиваемого контактного электрода и треханодного сегмента. Основной компонент легко заменяется. Это позволяет сокращать потери времени и оптимизировать плазмотрон под различные операции за счет замены сопел.
Благодаря эффективности и высокой производительности, используется для напыления покрытий на большие поверхности. Для мелких деталей не подходит в связи с большим пятном распыления.
Сравнение плазмотронов Delta со стандартными:
F4 / F6 / P2:
- Единственная дуга
- различные диаметры сопел
- колебание напряжения +/-20V.
- Одна каскадируемая дуга, стабилизированная как аксиально, так и радиально
- колебание напряжения +/-3V.
- Постоянная передача плазменной энергии радиально впрыскиваемым частицам порошка. Дуга равномерно распределяется на три анода.
- Не требуется корректировка положения порошковых инжекторов в зависимости от параметров напыления, т. к. положение трех оснований анодов сбалансировано радиально.
Технические характеристики:
- Обычно эксплуатируются с плазменными установками мощностью до 70 Квт
- Обычно эксплуатируются с плазмообразующими газами Ar/H2, для некторых материалов может применяться смесь Ar/He;
- Благодаря высокой производительности и эффективности рекомендуется для напыления покрытий на большие поверхности. Не лучший выбор для маленьких деталей - довольно большое пятно распыления.
Плазмотрон P2
Размещение анода и катода полностью совпадают, что позволяет использовать базовые параметры напыления. Главное преимущество установки — компактность, которая достигается за счет короткого электрода. Нестандартный дизайн позволяет избежать негативных последствий как для продолжительности жизни электрода, так и для качества плазмы. Рекомендуется увеличение температуры для максимизации продолжительности работы. Стоит отметить, что катоды и аноды стоят значительно дешевле, чем для F4.
Технические характеристики:
- Обычно эксплуатируются с плазменными установками мощностью до 55 Квт
- Обычно эксплуатируются с плазмообразующими газами Ar/H2, для некторых материалов могут применяться смеси Ar/He, Ar/N2 или N2/H2;
- Для увеличения качества напыления используются различные сопла: сопла Лаваля позволяют напыление с более высокими эффективностью и коeффициэнтом использования при пониженном уровне шума.
Общепринятая в авиации установка для осуществления напыления в отверстиях.
Обычно эксплуатируется с плазмообразующими газами Ar/H2. Совместим с плазменными установками мощностью до 500 А
Минимальный диаметр — 80 мм.
- Обычно эксплуатируются с плазменными установками мощностью до 500 А
- Обычно эксплуатируются с плазмообразующими газами Ar/H2,
- Минимальный диаметр - 80 мм
![]() |
Предназначен для напыления внутренних поверхностей диаметром от 90 мм. Техническая характеристика плазмотрона F1 |
Плазмотрон F7, для внутреннего напыления
Установка разработана для напыления внутренних поверхностей.
Отличается улучшенным энергопотреблением, обычно используется при силе тока до 600 A.
Есть возможность охлаждения обрабатываемой детали воздушными соплами, которые встроены непосредственно в устройство. Минимальный диаметр напыляемого отверстия - 90 мм.
Преимущества:
- Улучшенное по сравнению с F1 энергопотребление, обычно используется при силе тока до 600 A
- Возможность охлаждения напыляемой детали воздушными соплами, встроенными в плазмотрон;
- Минимальный диаметр напыляемого отверстия - 90 мм

Мощность изменяется в зависимости от выбранных катода и анода. Максимальная величина – 80 кВт.
Комплектуется удлинителем для напыления внутренних поверхностей.
Металлизация – эффективный способ придать конечному продукту дополнительные технические и эксплуатационные характеристики. Плазменное напыление представляет собой совершенный вариант диффузной обработки металлических поверхностей для создания качественного покрытия из другого металла или сплава. Диффузная металлизация позволяет улучшить твердость, прочность, цвет и антикоррозийные свойства исходной детали.
Отличительные особенности диффузного напыления
При работе с металлическими поверхностями часто возникает необходимость придать конечному продукту дополнительные характеристики, чтобы расширить область применения детали. Можно защитить металлическую поверхность от воздействия влаги, высокой температуры и агрессивной химической среды. Плазменное напыление имеет ряд особенностей, которые отличают процесс металлизации от других вариантов обработки металлических поверхностей:
- Ускоренный процесс нанесения покрытий благодаря высокотемпературному воздействию на обрабатываемую поверхность – порядка 5000-6000° C. Технологически напыление может длиться доли секунд для получения необходимого результата.
- Плазменная обработка металлов позволяет создать на поверхности комбинированный слой. Диффундировать можно не только металлические частицы, но и элементы газа из плазменной струи. В итоге металл насыщается атомами нужных химических элементов.
- Традиционная металлизация протекает неравномерно и характеризуется длительностью технологического процесса и возможными окислительными реакциями. Струя высокотемпературной плазмы создает равномерную температуру и давление, обеспечивая высокое качество финальных покрытий.
- При помощи плазменной струи перенос частиц металла и атомов газа происходит мгновенно. Процесс относится к области сварки с применением порошков, стержней, прутков и проволоки. Перенесенные частицы образуют слой толщиной от нескольких микрон до миллиметров на поверхности твердого тела.
Современная диффузная металлизация предполагает использование более сложного оборудования, чем в случаях, когда применяют газоплазменное оборудование. Для организации процесса диффузной обработки требуется одновременно наличие газовой и электрической аппаратуры.
Оборудование для диффузного воздействия
Ионно-плазменное напыление по поверхности металлов проводится с использованием высокотемпературной технической плазмы – совокупности большого количества частиц (квантов света, положительных ионов, нейтральных частиц, электронного газа). Под воздействием высокой температуры за счет электрических разрядов в газах происходит интенсивная термоионизация частиц, которые сложно взаимодействуют друг с другом и окружающей средой. Благодаря этому различают плазму, ионизированную слабо, умеренно и сильно, которая, в свою очередь, бывает низкотемпературной и высокотемпературной.
Создать необходимые условия для протекания процесса плазменной ионизации и обработки металлических покрытий помогает специальное оборудование – плазменные установки. Обычно для работы используется дуговой, импульсный или искровой электрические разряды.

Для реализации технологического процесса требуются следующие установки:
- Генератор высокочастотного типа (можно использовать сварочный преобразователь) – служит источником разряда.
- Герметизированная камера, в которую помещают детали для нанесения покрытий методом плазменного напыления.
- Газовый резервуар. В его атмосфере выполняется ионизация частиц под действием электрического разряда.
- Установка, создающая давление газа. Можно использовать вакуумную или насосную аппаратуру.
- Система, при помощи которой можно качественно изменять токовые характеристики, давление, напряжение, тем самым увеличивая или уменьшая толщину напыляемых покрытий.
Как происходит плазменное напыление: в герметизированной камере фиксируют обрабатываемую деталь, создают электрический разряд, прокачивают рабочую среду с необходимым давлением и напыляемыми порошковыми элементами. Образуется высокотемпературная плазма, которая переносит частицы порошков вместе с газовыми атомами на поверхность некоторой детали. При проведении диффузной металлизации в вакууме, в атмосфере инертного газа или при пониженном давлении можно увеличить скорость движения частиц и получить боле плотный и высокоадгезивный тип покрытий.
Где используют плазменную металлизацию
Поскольку напыляемым материалом может служить практически любой сплав или металл, ионно-плазменное напыление широко используют в различных отраслях промышленности, а также для проведения ремонтно-восстановительных работ. Любой металл в виде порошков подается в плазменные установки, где под воздействием высокотемпературной плазмы расплавляется и проникает в обрабатываемую металлическую поверхность в виде тонкого слоя напыления. Сферы применения диффузной металлизации:
- детали для авиационной, космической и ракетной промышленности;
- машиностроительное оборудование и энергетическая отрасль;
- металлургическая и химическая отрасль промышленности;
- нефтедобывающая, нефтеперерабатывающая и угольная отрасль;
- транспортная сфера и производство приборов;
- ремонт и реставрация машин, оборудования, изношенных деталей.
Когда струя плазмы и порошков проходит по электродуге и осаживается на обрабатываемой поверхности, образованный слой приобретает важные качественные и эксплуатационные характеристики:
- жаростойкость;
- жаропрочность;
- коррозийную устойчивость;
- электроизоляцию;
- теплоизоляцию;
- эрозийную прочность;
- кавитационную защиту;
- магнитные характеристики;
- полупроводниковые свойства.
Ввод напыляемых порошков в установки осуществляется с плазмообразующим или транспортируемым газом. Плазменное напыление позволяет получать различные типы покрытий без ограничения по температуре плавления: металлы, комбинированные сплавы, карбиды, оксиды, бориды, нитриды, композит. Материал, который обрабатывается в установках, не подвергается структурным изменениям, но поверхность изделия приобретает необходимые качественные характеристики. Напылять можно комбинированные слои (мягкие и твердые), тугоплавкие покрытия, различные по плотности составы.
Варианты плазменной металлизации
Для нанесения на металлическую поверхность некоторого слоя напыления в условиях высокотемпературной плазменной среды в качестве формирующих покрытий используют не только порошковые составы. В зависимости от того, какими свойствами должна обладать обработанная поверхность, используют следующие особенности плазменной металлизации:
- Наплавление высокоуглеродистой или легированной проволокой под флюсом. Для восстановления поверхностей используют наплавку в установках стержневым или пластинчатым электродом.
- Наплавка по порошковому слою под флюсом используется для реставрации деталей с обширными деформациями по окружности с толщиной слоя более 2 мм.
- Установки для напыления пропускают в качестве плазмообразующих газов аргон, азот, водород, гелий либо их смеси. Необходимо обеспечить отсутствие кислорода, чтобы исключить окисление наплавляемых покрытий.
Наиболее часто этот вид обработки используют для восстановления различных деталей при ремонте автомобильных двигателей. Так, при помощи диффузной металлизации удается восстановить отверстия коренных опор в блоках цилиндров (распространенная поломка), устранить износ головок цилиндров, реставрировать поршни из алюминиевого сплава, коленчатые валы из высокопрочного чугуна, ролики, катки.
При использовании ионно-плазменного напыления значительно возрастает износостойкость сложных узлов оборудования, механизмов и установок. Диффузная металлизация – это эффективный метод реставрации изношенного и усталого металла, а также оптимальный процесс для задания металлическим поверхностям необходимых прочностных и эксплуатационных характеристик.
Это прогрессивный способ нанесения покрытий, при котором расплавление и перенос материала на восстанавливаемую поверхность осуществляется струей плазмы. Плазма - это сильно ионизированное состояние газа, когда концентрация электронов и отрицательных ионов равна концентрации положительно заряженных ионов. Плазменную струю получают, пропуская плазмообразующий газ через электрическую дугу при ее питании от источника постоянного тока напряжением 80-100 В.
Переход газа в ионизированное состояние и распад его на атомы сопровождается поглощением значительного количества энергии, которая выделяется при охлаждении плазмы в результате ее взаимодействия с окружаемой средой и напыляемой деталью. Это обуславливает высокую температуру плазменной струи, которая зависит от силы тока, вида и расхода газа. В качестве плазмообразующего газа обычно применяют аргон или азот и реже водород или гелий. При использовании аргона температура плазмы составляет 15000-30000°С, а азота - 10 000-15 000 °С. При выборе газа следует учитывать, что азот дешевле и менее дефицитен, чем аргон, но чтобы зажечь в нем электрическую дугу, требуется значительно большее напряжение, что обуславливает повышенные требования к электробезопасности. Поэтому иногда при зажигании дуги используют аргон, для которого напряжение возбуждения и горения дуги меньше, а в процессе напыления - азот.
Покрытие формируется за счет того, что поступающий в струю плазмы наносимый материал расплавляется и переносятся потоком горячего газа на поверхность детали. Скорость полета частиц металла составляет 150-200 м/с при расстоянии от сопла до поверхности детали 50-80 мм. Благодаря более высокой температуре наносимого материала и большей скорости полета, прочность соединения плазменного покрытия с деталью выше, чем при других способах металлизации.
Высокая температура и большая мощность по сравнению с другими источниками тепла является основным отличием и преимуществом плазменной металлизации, обеспечивающим значительное повышение производительности процесса, возможность расплавлять и наносить любые жаростойкие и износостойкие материалы, включая твердые сплавы и композиционные материалы, а также оксиды, бориды, нитриды и др., в различных сочетаниях. Благодаря этому можно формировать многослойные покрытия с различными свойствами (износостойкие, хорошо прирабатывающиеся, жаростойкие и др.). Наиболее качественные покрытия получаются при применении самофлюсующихся наплавочных материалов.
Плотность, структура и физико-механические свойства плазменных покрытий зависят от наносимого материала, дисперсности, температуры и скорости столкновения переносимых частиц с восстанавливаемой деталью. Последние два параметра обеспечиваются за счет управления плазменной струей. Свойства плазменных покрытий существенно повышаются при последующем их оплавлении. Такие покрытия эффективны при ударных и высоких контактных нагрузках.
Принцип работы и устройство плазмотрона иллюстрирует рис. 4.51. Плазменную струю получают, пропуская плазмообразующий газ 7 через электрическую дугу, создаваемую между вольфрамовым катодом 2 и медным анодом 4 при подключении к ним источника тока.
Катод и анод разделены между собой изолятором 3 и непрерывно охлаждаются жидкостью б (желательно дистиллированной водой). Анод выполнен в виде сопла, конструкция которого обеспечивает обжатие и определенное направление плазменной струи. Обжатию способствует также электромагнитное поле, возникающее вокруг струи. Поэтому ионизированный плазмообразующий газ выходит из сопла плазмотрона в виде струи небольшого сечения, что обеспечивает высокую концентрацию тепловой энергии.
Рис. 4.51. Схема процесса плазменного напыления: 1 - порошковый дозатор; 2- катод; 3 - изоляционная прокладка; 4 - анод; 5 - транспортирующий газ; 6 - охлаждающая жидкость; 7 - плазмообразующий газ
Наносимые материалы используются в виде гранулированных порошков с размером частиц 50-200 мкм, шнуров или проволоки. Порошок может подаваться в плазменную струю вместе с плазмообразующим газом или из дозатора 1 транспортирующим газом 5 (азотом) в сопло газовой горелки, а проволоку или шнур вводят в плазменную струю ниже сопла плазменной горелки. Перед использованием порошок следует просушить и прокалить для уменьшения пористости и повышения сцепляемости покрытия с деталью.
Защита плазменной струи и находящихся в ней расплавленных частиц металла от взаимодействия с воздухом может осуществляться потоком инертного газа, который должен охватывать плазменную струю. Для этого в плазмотроне концентрично основному предусматривается дополнительное сопло, через которое подается инертный газ. Благодаря ему исключается окисление, азотирование и обезуглероживание напыляемого материала.
В рассмотренном примере источник питания подключен к электродам плазмотрона (закрытая схема подключения), поэтому электрическая дуга служит только для создания плазменной струи. При применении наносимого материала в виде проволоки источник питания может быть подключен также и к ней. В этом случае кроме плазменной струи образуется плазменная дуга, которая также участвует в расплавлении прутка, благодаря чему мощность плазмотрона существенно возрастает
Современные плазменные наплавочные установки имеют электронные системы регулирования параметров процесса, оснащаются манипуляторами и роботами. Это повышает производительность и качество процесса напыления, улучшает условия работы обслуживающего персонала.